
Supporting Product Quality at YKK AP — The Role of the Field Engineer, from Installation Support to Gathering Feedback from Work Sites and Making Improvements
YKK AP believes that, as a manufacturer, its role is not only to make and sell products, but also to take responsibility for ensuring that the products are installed correctly and demonstrate their value throughout their life cycle at the customer’s end. It is Field Engineers (FE) that put this approach into practice on the front lines. In this article, Toshiaki Yamamoto, Director of the Field Technical Center, the headquarters organization of the FE Group, spoke to us about the role and importance of FEs, while Tooru Ueki and Tsukasa Sunazawa, two members of the FE Group, told us about their specific activities and thoughts on their work.
What are “Field Engineers”?
Holding responsibility for installation quality, FEs form a technical group that works to improve on-site issues, leading to product improvements.
To explain the role of Field Engineers, let us first take a look at the Field Technical Center (FTC). The FTC is engaged in a wide range of activities, including the development of installation jigs to make the installation of products easier and reduce the workload involved, verifying the installation of new products, providing technical support to enhance architectural product distributors’ competitiveness, and providing training and guidance on assembly, delivery, and other areas to ensure product quality is maintained. FEs are engineers who are assigned to the FTC and work on the front lines at installation sites. There are currently 39 FEs at YKK AP, working at 13 locations nationwide. The FE Group also provides technical support for the installation of vinyl windows and remodeling and exterior products, conducts quality audits of distributors, and identifies areas for product improvement and provides feedback to the FTC. When the position that preceded FE was first established around 2000, its role was very different from that which FEs play today. At that time, they were responsible for assembling sashes to make finished windows, and the assembly know-how they developed through this experience laid the foundation for their current work, such as making proposals for operational improvements to distributors. The role then changed over time, and there was a period when the focus was on product maintenance and investigating the causes of defects. As such, they would handle consultations such as locks not working on a site-by-site basis, but realizing that defects would not decrease without addressing the root of the problem, it was decided to enhance technical support, such as installation training sessions for installers, thereby preventing defects from occurring in the first place. As a result, since 2016, "technical support" has accounted for more of their work than "defect investigations," now comprising about 80% of the total.
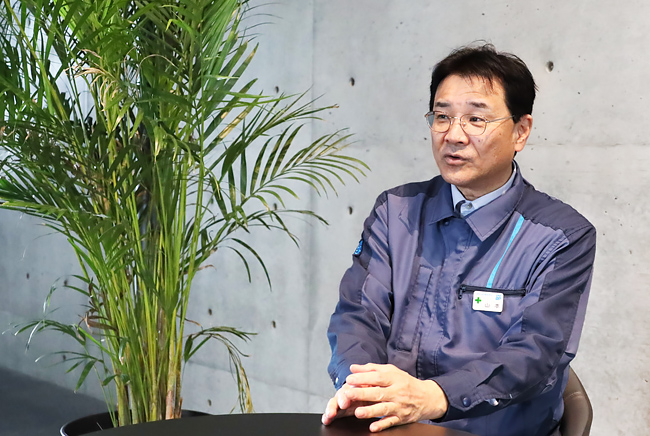
Director Yamamoto explains the FTC and FEs
At the heart of our technical support and problem solving is our belief that, as a manufacturer, we not only make products, but handle everything up to installation. We have a strong sense of responsibility towards the sites where our products are used, which means that we are responsible not only for shipping the products, but also for ensuring that they are installed correctly and perform to their full potential.
Specific activities of the FE Group: Responding to feedback on installation sites
The work of FEs covers a wide range of activities, but the focus is always on the worksites and feedback from customers.
Product installation training sessions and support at installation sites
In order to ensure that the products are installed correctly to perform to their full potential, training sessions are held approximately 1,800 times a year throughout Japan for carpenters, distributors, and others who actually install the products to teach them methods for doing so. In particular, the installation of inner windows, a remodeling product, has seen an increasing number of entrants from different industries due to subsidies provided by the Housing Energy Conservation Campaign (*) a joint initiative between the Ministry of Land, Infrastructure, Transport and Tourism, the Ministry of Economy, Trade and Industry, and the Ministry of the Environment, which has been running since 2023. Accordingly, training sessions using actual products are held at YKK AP’s training facilities or at the installer’s offices, allowing installers new to handling inner windows to perform on-site surveys and installations correctly. FEs also travel to the work sites of first-time installers, providing support from behind the scenes to address any worries they might have.
Participants learning enthusiastically at a training session on the installation of inner windows
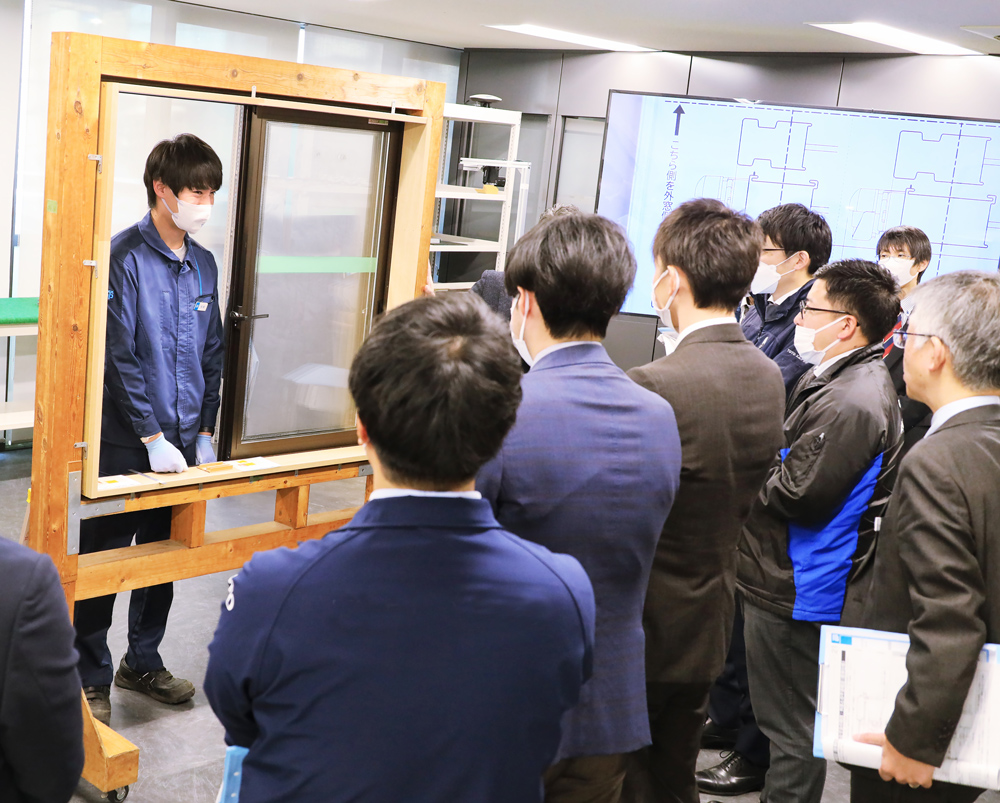
Explanation using actual products
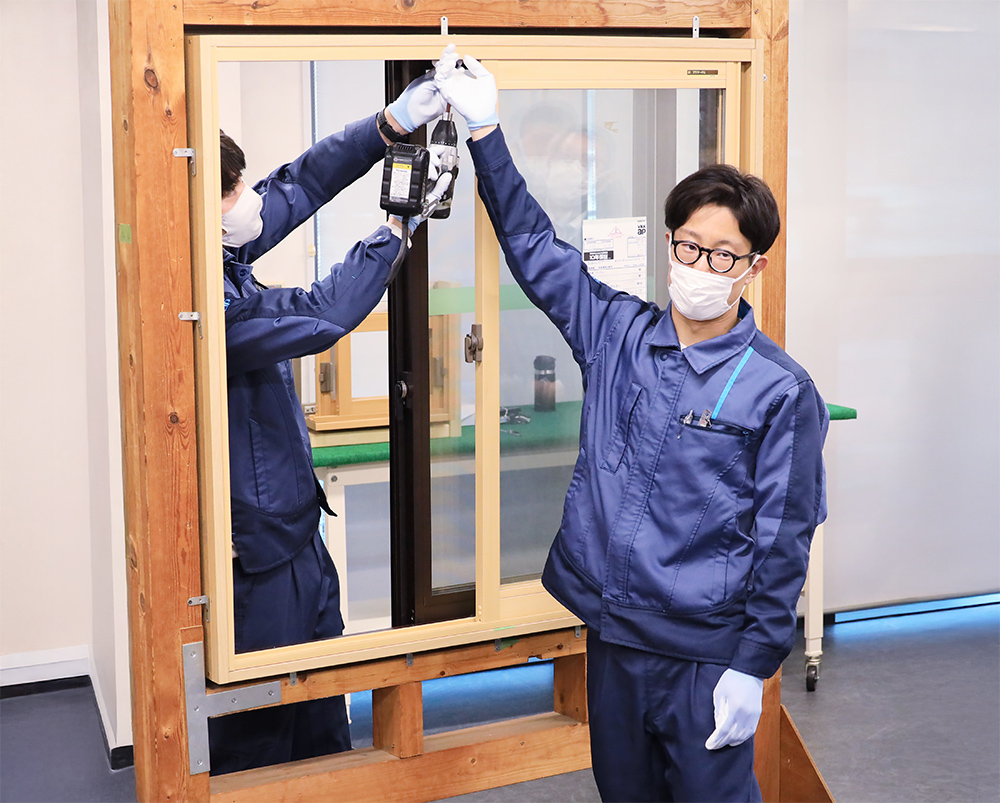
Gathering real feedback from the field to improve products
Training sessions and dialogue at installation sites allow FEs to gather valuable on-site information directly from installers, such as issues related to product handling and construction, as well as requests for improvement. Regarding dialogue with installers, Mr. Ueki said, "We have very close relationships with contractors and distributors, so we are able to get direct feedback from them. That feedback is sometimes quite critical, but on the other hand, it is always rewarding for us as FEs to receive words of gratitude for the improvements we make." All of this information is gathered together at the FTC and used in conjunction with information on past problems to confirm quality targets during development reviews of new products.

Mr. Ueki talks about the rewarding aspects of being an FE
One example of a product improvement Mr. Ueki was involved in is a change in the shape of the metal tabs for preventing fixed windows installed in rows from falling out. With the original specifications, when the glass was placed into a row of fixed windows, there was a risk that the glass would strike the metal tabs installed earlier, causing it to break. To address this, they raised a request for improvement and the shape of the tabs was changed, allowing them to be attached after the glass was inserted. This reduced the risk of the glass hitting the tabs when inserted, reducing the risk of breakages and improving workability.
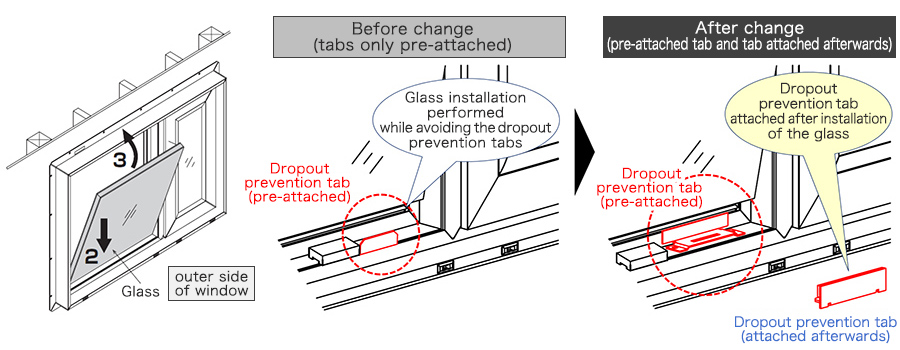
Director Yamamoto says, "We are not only looking at installation, but also the products themselves. FEs gather feedback from the field, and the FTC collates this information, discusses product development and product improvement, and takes part in product installation and improvement. If necessary, we ask for changes in the shape of the product to make installation safer and more efficient. We also make jigs to support installation. We want to always be there for our installers, and although it might seem presumptuous for me to say, I think we have helped make things easier for them.
Proposing improvements to installation methods
To address customer issues, FEs will not only suggest improvements to products, but sometimes suggest appropriate installation methods. For example, Mr. Sunazawa received feedback saying that the cutting-out process ( manual processing such as cutting parts of components ) for installing screen rails on vinyl windows was difficult, and when he actually tried it himself, he realized how difficult it was: the cutter blade would jump out of alignment, often causing damage to the window. To address this, he thought up a safer and more efficient method using marking calipers, and proposed it to the installer, to their satisfaction. In this way, FEs work to solve on-site issues, including proposals to ensure greater safety and efficiency, such as changing the installation method or the tools used.
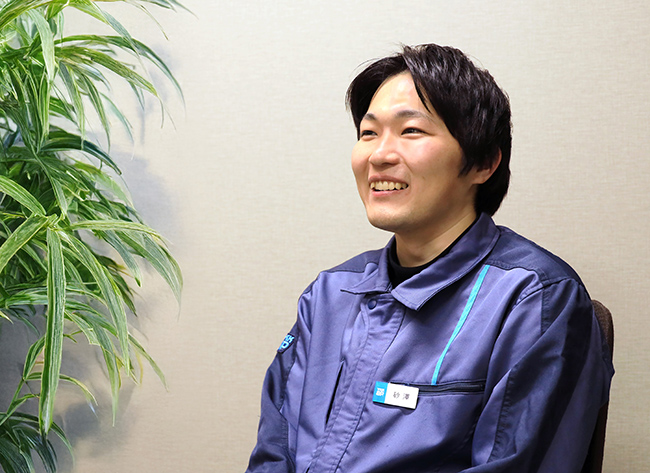
Mr. Sunazawa discussing making proposals for installation methods
FEs’ activities support operational efficiency and ensure safety for installers by not only responding to on-site situations but also improving installation methods, improving products, and developing jigs as work aids. In turn, this helps guarantee quality and improve the reliability of YKK AP products. What underlies these activities is FEs’ commitment to listening to customers and thinking from the installer’s point of view.
Striving to be engineers who can deliver excitement for customers
Thanks in part to FEs’ activities and product improvements, the number of defects has steadily declined over the nine years since 2015, reaching a reduction of approximately 80% by FY2024, leading to increased customer satisfaction and trust in the YKK AP brand. Regarding his future aspirations, Mr. Ueki says "Through FE activities, I would like to provide safety and a sense of security to our customers, and to ensure that both the installer and the owner are satisfied that they chose YKK AP products.
To address the issue of the shortage of installers that the entire construction industry is facing, a result of the aging population, consideration is also being given to the use of digitalization and AI. Center Director Yamamoto says of his goal, "I want to pass on to my successors what my predecessors passed on to me, and to nurture technicians with field experience who can deliver excitement for customers."
FEs are the ones who keep in close contact with installers on the front lines, listen to what they have to say, and contribute to maximizing product value and resolving issues on the ground. Their activities enable YKK AP to fulfill its responsibilities from manufacturing to on-site installation, leading to greater satisfaction on the part of every customer, thereby further improving corporate value.
(*) A collective term for subsidy schemes that, with the aim of strongly promoting energy conservation in the residential sector to achieve carbon neutrality by 2050, provide support for energy conservation in residential buildings, such as by improving the thermal insulation performance of houses and installing high-efficiency water heaters.
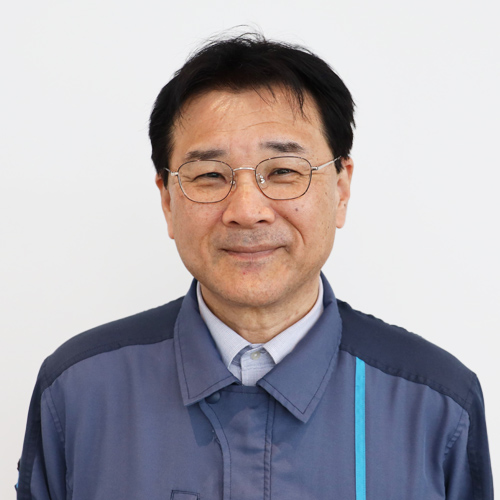
Toshiaki Yamamoto
Yamamoto joined YKK in 1984. Since then, he has worked on production lines, equipment maintenance, and fabrication technology. Since FY2020, in his current position at the YKK AP Fabrication Technology Department, he has been overseeing the FTC and all FEs.
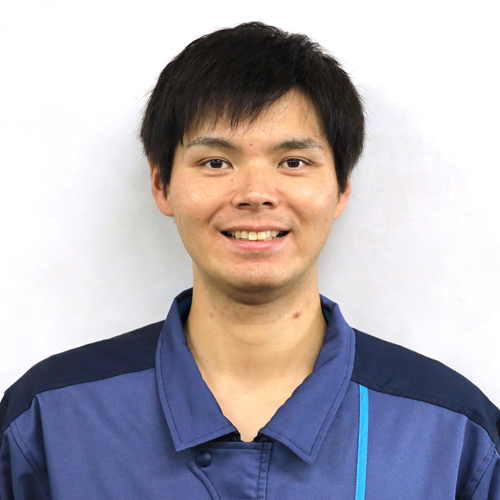
Tooru Ueki
Ueki joined YKK AP in 2007. Since then, he has worked for 17 years as an FE in locations including Chiba, Saitama, and Niigata. He hopes to continue building up his experience in the field to become a specialist as an FE.
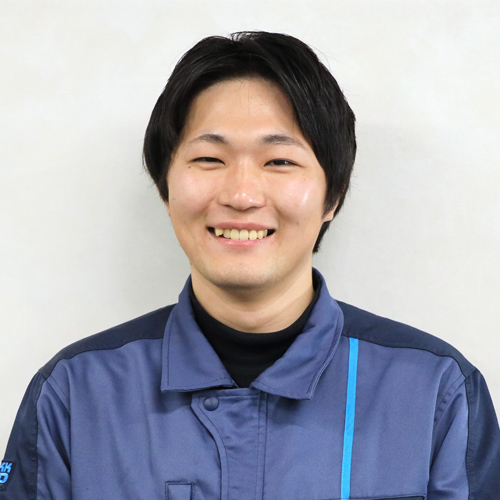
Tsukasa Sunazawa
Sunazawa joined YKK AP in 2017. After six years at the FTC, he has been working as an FE since 2023. Going forward, he hopes to become a leader who can unite the work area.
Share this article
- SNS Link X X Share
- SNS Link Facebook Facebook Share
- SNS Link LinkedIn LinkedIn Share
- SNS Link LINE LINE Share
- Copy Link Copy Link Copy Link Copied Link
Related stories
-
The installation training network began as a challenge to solve the shortage of sash and curtain wall installation technicians. Taking on challenges in collaboration with partners, and going from Japan to overseas
- Technology
- Installation
- Solving Social Issues
- Story of Project
-
Establishing a digital R&D center in the U.S.A. What is YKK AP's digital strategy for smart factories?
- R&D
- Technology
- Installation
- DX
-
By bringing installation technician expertise and monozukuri together, YKK AP is focusing on human resource and product development to enhance exterior product quality and streamline installation.
- Exterior Business
- R&D
- Installation
- Solving Social Issues